Solid recovered fuel (SRF) is non-hazardous waste, such as paper, plastics, textiles, or wood, that can be burned as fuel and that meets certain quality specifications. Obtaining energy from waste materials can provide several environmental benefits, such as reducing the use of fossil fuels and keeping waste out of landfills.
Measurlabs offers a comprehensive range of SRF testing services to help companies ensure the fuel they produce or plan to use meets all applicable quality standards – and that associated emissions are calculated correctly, in compliance with regulations such as the EU Monitoring and Reporting Regulation (MRR).
SRF definition and classification
SRF is a subset of refuse-derived fuel (RDF), which is solid, non-hazardous waste that can be burned as energy. To be classified as SRF, refuse-derived fuel must meet the technical specifications outlined in standard EN ISO 21640. In addition, SRF might need to meet supplementary standards in some European countries or some commercial contexts.1
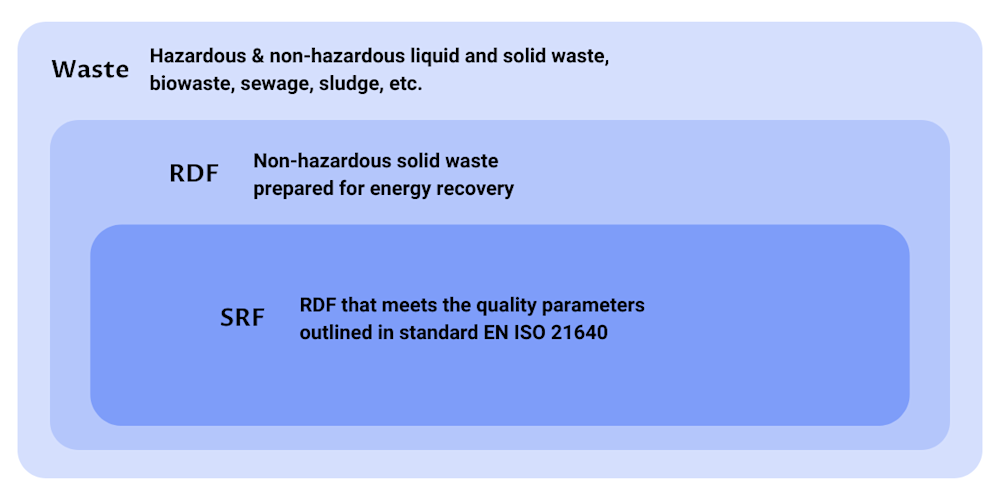
EN ISO 21640 classifies SRF into five classes based on net calorific value (NCV) and chlorine and mercury content. The class criteria that solid recovered fuel should match depend on its intended application. For example, the cement industry often requires class 1 or 2 SRFs, while class 3 and 4 fuels are more commonly used in the pulp and paper industry and chemical industry.
Table 1: Classes of SRF according to EN ISO 216403
Classification characteristic | Unit | Class 1 criteria | Class 2 criteria | Class 3 criteria | Class 4 criteria | Class 5 criteria |
Net calorific value (mean) | MJ/kg | ≥25 | ≥20 | ≥15 | ≥10 | ≥3 |
Chlorine (Cl) content (mean) | % in mass (dm) | ≤0.2 | ≤0.6 | ≤1.0 | ≤1.5 | ≤3 |
Mercury (Hg) content (median) | mg/MJ | ≤0.02 | ≤0.03 | ≤0.05 | ≤0.10 | ≤0.15 |
Mercury content (80th percentile) | mg/MJ | ≤0.04 | ≤0.06 | ≤0.10 | ≤0.20 | ≤0.30 |
Treatment of SRF under EU emissions trading
In the EU Emissions Trading System (ETS), CO2 emissions are priced differently depending on the origin of the carbon. The emission factor of sustainably sourced biomass is zero, which means that CO2 emission certificates are only needed for the fossil fraction of total emissions caused by the burning of SRF.4 The biomass fraction of CO2 emissions can be determined through radiocarbon analysis to ensure accurate monitoring and reporting under EU ETS.
What are the challenges with using SRFs?
Recovered fuels have more variation than traditional fuels in their physical properties and chemical composition. Common technical challenges resulting from this include:5
Insufficient or inconsistent energy content, making it difficult to reliably achieve the targeted temperature.
Excessive moisture content, which may negatively affect net calorific value, grinding, and pulverization.
Elemental contaminants, which may cause undesired byproducts during the process. Some examples include:
Chlorine, which can form byproducts that negatively affect processing equipment
Sulfur, phosphorus, and metal oxides, which can lower the quality of the product in some industries
Mercury, which can cause various environmental and human health issues following the combustion process.
Failure to meet physical requirements in terms of particle size, shape, or density, leading to partial combustion or damage to the processing system.
Overcoming these challenges requires robust quality control throughout the SRF production process.
Standardized testing to determine SRF quality
Some of the most common SRF quality parameters, the standard methods for determining them, and the criteria the fuel must meet in terms of each parameter to be used in certain key applications are outlined below:6
Energy content (net calorific value, NCV) can be determined using ISO 21654.
Uses bomb calorimetry tailored to the composition and properties of SRF, supersedes EN 15400.
Coal plants usually require SRF with a calorific value greater than 11 MJ/kg, while the main burner in the cement industry requires an NCV of over 21 MJ/kg.
Moisture content is often determined by CEN/TS 15414-1.
Uses an oven drying method specifically for SRF, based on EN 14774 for solid biofuels.
Some industrial applications require very low moisture content SRFs, such as about 7–12% for a lime kiln, while others can handle more moisture, such as 20–50% for lignite dry-bottom boilers in coal-fired power plants.
Ash content can be determined by ISO 21656.
Involves measuring the residual ash after complete combustion of the SRF, supersedes EN 15403.
The requirements vary from <2–10% of dry matter in lime kilns to <15–30% in coal-fired power plants, with the more specific limit depending on furnace technology.
A carbon, hydrogen, nitrogen, and sulfur (CHNS) analysis is often performed by ISO 21663.
Measures the target elements by the instrumental method, supersedes EN 15407.
The sulfur content of SRFs must be below certain parameters in the lime and waste-to-energy (WtE) sectors.
Sulfur, chlorine, fluorine, and bromine content can be determined following EN 15408.
Involves measuring the resulting gas after complete combustion, supersedes CEN/TS 15408.
The resulting chlorine measurement is one of the main components of the SRF classification system.
One partner for all your SRF testing needs
Measurlabs offers every analysis needed to classify solid recovered fuels, verify their suitability for specific burners, and calculate resulting emissions in compliance with the EU Emissions Trading System. Our most popular SRF tests include the following:
Standard SRF analysis package, which covers moisture, ash, net calorific value, CHNS(O), and 13 heavy metals
Biogenic carbon analysis based on the radiocarbon method to determine the biomass fraction for EU ETS reporting
Additional tests to determine further parameters, such as particle size distribution and sulfur and halogen content.
Contact us with a brief description of your samples and objectives, and we will prepare a tailored quotation, factoring in any volume discounts available for your sample volumes.
References
1 Austria, France, Germany, and Italy have additional quality requirements. See 8.1.3, Other national quality classifications, in European Investment Bank’s (EIB) guideline Managing refuse-driven and solid recovered fuels: Best practice options for EU countries.
2 The figure is adapted from Figure 1 in section 2.1 of the EIB guideline on Managing refuse-derived and solid recovered fuels.
3 Based on ISO 21640:2021, Table 2 – Classification of solid recovered fuels.
4 See Commission Implementing Regulation (EU) 2018/2066 on the monitoring and reporting of greenhouse gas emissions, especially Article 38 on biomass source streams and Article 39 on determining the biomass fraction.
5 See section 2.5 in the EIB guideline.
6 The industry-specific requirements are based on Table 3 in section 2.5 of the EIB guideline.